案例6: 润滑油化验——液压系统故障分析
某制造企业一台磨床的,液压阀出现了运转不畅,怀疑是因为系统液压油已使用二年,可能是油品失效引发的故障,所以决定换油。但重新换了同牌号的32#抗磨液压油,仅过2天,便发生了液压阀门卡死的停机事故。经折检发现阀芯内外均粘附有一层黄色粘稠的胶状物。阀门、阀芯经清洗重新装配后,开机不到30分钟再次发生卡死现象。用户将新油、在用油及阀门上粘附的胶状物三个样品同时送到专业实验室检测,要求对阀门堵死故障进行诊断,检测单位对三个样品分别做了红外光谱分析、光谱元素分析、微水、酸值测试、滤膜分析等,测试结果(见表1)
表1 样品检测项目及结果
| 新油 | 在用油 | 胶状污染物 |
外观 | 黄色透明 | 黄色浑浊、有颗粒物 | 黄色粘稠 |
水分 mg/kg | — | 49 | — |
总酸值 mgKOH/g | 1.07 | 0.68 | — |
元素分析 mg/kg Zn P | 692 545 | 452 360 | __ __ |
红外光谱分析 | 矿油型液压油 (见图1) | 与新油相符 (见图2) | 3405 cm-1、1712 cm-1、1607 cm-1、1168 cm-1、1068cm-1吸收峰较强与新、旧油明显不同(见图3) |
滤膜分析 | — | 有大量黑色污染颗粒和非金属污染手 | — |
根据上述化验分析结果,得出如下结论:
1、 红外光谱分析显示,新油和在用油化学组分基本相同(见图1-2)。在用油外观虽然浑浊,且目测有颗粒污染,但红外光谱分析未发现本质变化。
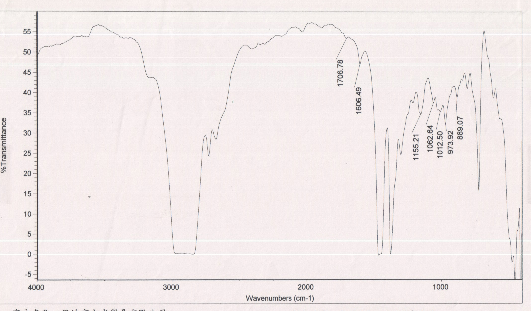
图1 新油红外光谱图
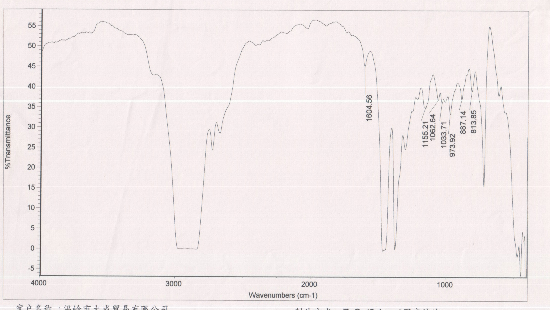
图2在用油红外光谱图
2、在用油的酸值及元素Zn、P含量明显低于新油。一般情况下新油在使用初期酸值下降是正常的变化趋势,但本案例中新油仅使用2天,酸值即大幅下降是不正常的。经向客户了解,新油和在用油确属同批次、同牌号油,新油取自油桶,在用油取自油箱。故怀疑在用油中可能混入了碱性化合物。为证实这一推测,进行了现场查证,查证结果发现,由于密封系统泄漏,有少量碱性磨削液混入了液压油中,因混入量不多,所以红外光谱图未见明显差异,但酸值和元素Zn、P含量差别却较大。
3、 对取自阀门上的胶状污染物,做了红外光谱分析(见图3),结果显示这些
胶状物的化学组成与新油和在用油明显不同。
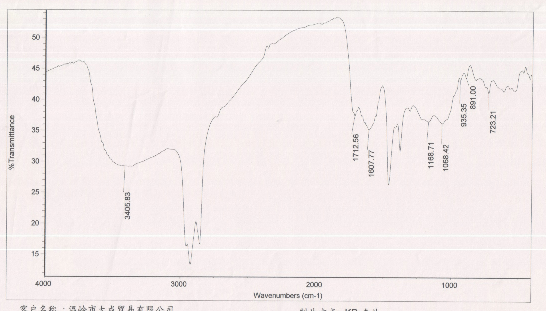
图3 胶状污染物红外光谱图
其谱图与新、旧油明显不同。在3405cm-1、17125cm-1、1607cm-1、1168 cm-1、1068 cm-1等处有较强的吸收峰,这些峰在液压油中均不存在,其特征表明是一种含羟基和表面活性剂的化合物。考虑到样品取自磨床液压阀门系统,推断这些胶状物是混入油中的磨削液与液压油发生化学反应生成的。(因样品量太少,无法进一步分析)。
4、在用油经滤膜分析,油中有较多黑色污染颗粒和非金属污染颗粒,这些污染物均来自外界污染,由于这些污染物而导致油样外观混浊。
根据以上分析,建议用户彻底清洗液压系统和油箱,并对清洗油进行污染度测试检验,合格后再重新加入装机油。
通过本案例润滑油化验分析可以看出,液压油污染控制对液压系统及元件的正常运行影响极大,在大修或换油时都应特别注意系统的清洗问题及系统密封状态的检查与控制。